Challenging Technology: The New F1 Car
by Cliff Hodges
Table of Contents
Formula One is a racing series steeped in tradition, offering exciting, high-speed open-wheel racing with a mix of elegance that attracts cultural elites and motorsport enthusiasts alike. What is often misunderstood is the sophistication and highly technical realm in which the teams and organization (FiA) operate. Formula One has been a world leader in innovation, so much so that their technology is being used in the private sector. Their innovations in battery cell efficiency, thermal management techniques, and aerodynamics are being used in various fields, including medical, automotive, and aeronautics. While individual teams have been leading these advancements due to their desire to be faster than their competitors, one could argue that the FiA (Formula One’s governing body) has established a framework of innovation within which the teams operate.
One of FiA’s missions is to provide close, entertaining racing while maintaining safety for drivers, teams, and fans. The FiA continues to improve vehicle performance to further promote their overall mission. The biggest examples thus far are the changes being made to the 2022 Formula One car.
Let’s dive in…
We will get to the changes in the 2022 Formula One car later. But first, let’s explore some basic fundamentals.
The Car
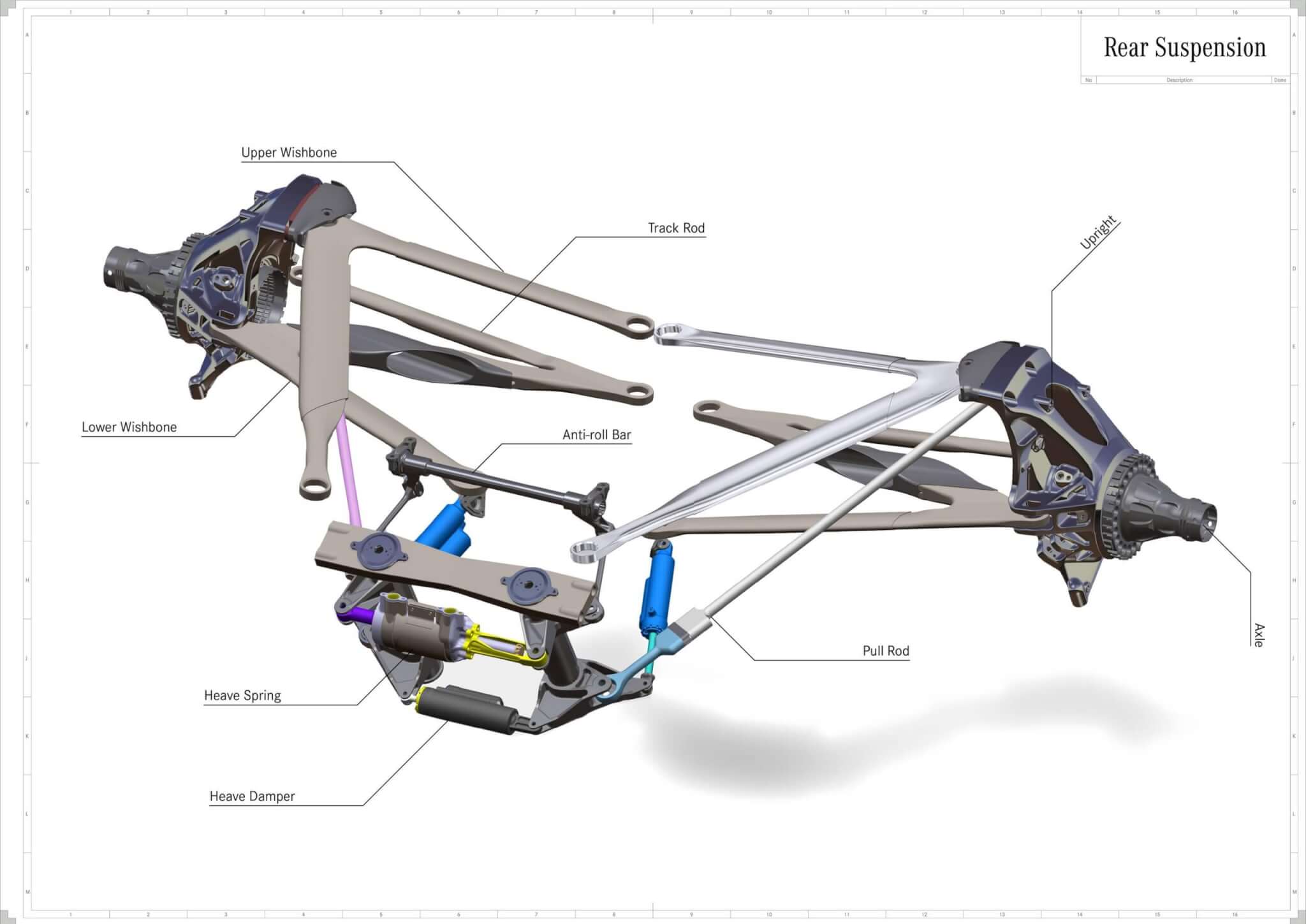
In vehicle dynamics, suspensions are designed to stabilize the vehicle under specifically defined conditions, such as cornering and braking maneuvers. The intended response of the system is to optimize grip at the ground level, which is generated through either mechanical or aerodynamic means. Mechanical grip considers tri-axial forces acting on the vehicle, assuming the tires and suspension are one system, without considering aerodynamic effects. Suspension geometry, travel, and flexibility is constructed to ensure chassis balance, intended to maximize vehicle load and contact patch interface. In general, there are various numbers of suspension types with an infinite number of component combinations that can be used for vehicle development. Thus, the type of suspension will be dependent on the vehicle as well as the racing series. For instance, NASCAR stock cars and late models use an independent front and rear suspension system with a spring and shock in either a coil over or separate spring and shock configuration. Formula One cars also use independent front and rear suspension systems that utilize double wishbone configurations (as seen in NASCAR suspensions). However, Formula One cars use push and pull rods connected to an anti-roll torsion bar as well as a heave spring and damper to control the amount of travel (Figure 1). The chosen suspension configuration is designed to respond to dynamic movements of the vehicle—such as roll, pitch, and yaw—to optimize chassis balance. Longitudinal and lateral weight transfer are examples of dynamic movements that are controlled by the suspension system. Lateral weight transfer in cornering is calculated using the geometry of the suspension or the angles of the suspension components to estimate roll center, and couples it with the vehicle’s center of mass (CoM) to understand the inertial effects on the vehicle. Ground-level roll center may seem optimal, but this creates a greater difference between roll center and the CoM, thereby increasing the magnitude of the moment at the center of the vehicle. Anti-roll bar systems are implemented to mitigate the severity of the moment and optimize weight transfer to reach ideal cornering load and speed combinations. Calculating longitudinal weight transfer can be treated in the same manner whilst suspensions are adjusted to find the right balance. Tracks containing more straight-line braking and acceleration zones may favor more balance in the longitudinal (pitch) direction as opposed to cornering (roll).
Aerodynamics refers to the shape of the body and how it moves through the air. Vehicle bodies are designed in such a way that the airflow literally forces the car toward the track surface, analogous to the inverse where airplane bodies are designed to keep the craft in the air. The design of the underbody and its channels, in conjunction with the rear diffuser extracting the air, is where a large part of the downforce is generated. This “Ground Effect” enables these vehicles to go extremely fast while maintaining vertical and lateral stability. The same is true in cornering and straight-line braking instances where aerodynamic forces are exerted on the vehicle and add to the summation of grip. While suspension components and dynamic responses are important for vehicle control, aerodynamic optimization becomes priority at speeds above 200 kph. Therefore, suspension configurations and setups are chosen to benefit their aerodynamic package. Most of the Formula One suspension components are open to airflow, as opposed to NASCAR suspensions that are primarily hidden from outside airflow and contribute little to no aerodynamic drag as a result. Essentially, tradeoffs in the vehicle’s dynamic performance tend to always favor aerodynamics.

So, why are the vehicle’s dynamics important? Vehicle response requires knowledge of the entire system and how it is affected from the ground up. This knowledge begins with tire response and how it is coupled with the vehicle’s suspension.
The Tire
Cornering stiffness (CS) is one of the most useful quantities in determining cornering ability. Expressed in Newtons per degree of slip angle, this measures the lateral force generated by the tire in the linear region (Figure 3 illustrates load sensitivity on CS). Plotting these results, one can see that the trend is linear up to a specific load (different for every tire). As the vertical load increases, the CS will usually either flatten the trend or decrease, indicating that the tire may have an optimal vertical load that maximizes CS. Looking back at vehicle weight transfer, this becomes a very important factor when identifying the tire’s peak performance. After all, the tire is the vehicle’s connection with the road, so tire response will resonate with and directly affect the vehicle’s performance. Tire thermal properties also play a major role in its performance. Increasing the tire’s external and internal temperature will often increase grip and peak lateral force. The trickier part about the tire’s thermal state is that increasing heat further activates the rubber compound, making it more pliable. Results from this additional flexibility are shifts in the contact patch (conforming to the specific driving pattern), blistering, or tread loss, which can also reduce the tire’s peak performance. Due to the extreme brake heat that F1 cars produce, methods are implemented to transfer this heat to the tires, which must also play a role in controlling the tire’s thermal state. Therefore, tire temperatures are monitored carefully throughout the race to preserve life and performance.
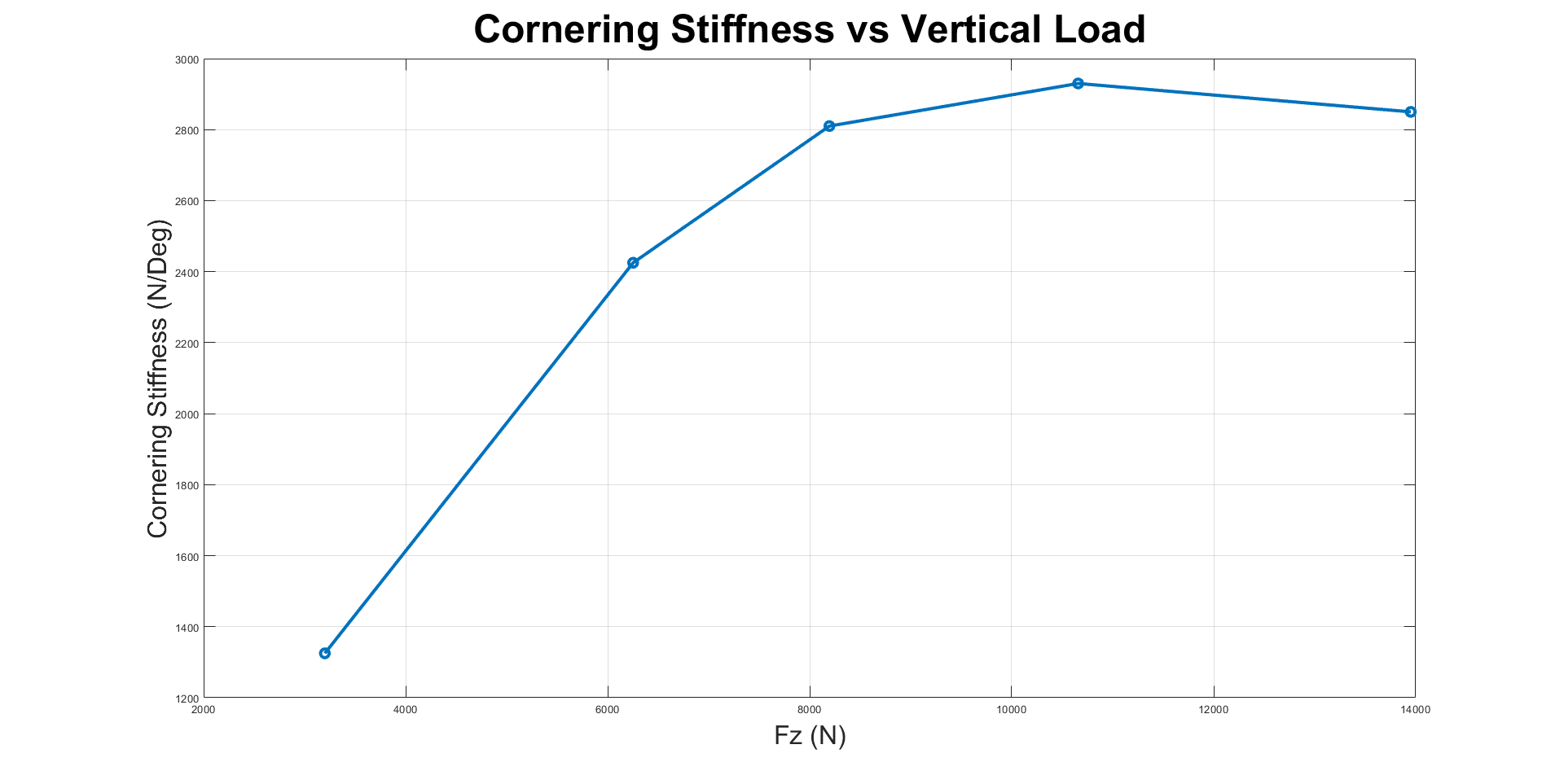
What does this mean for the new F1 designs?
New Aero Design
The new aerodynamic design of the car intends to reduce the effect of dirty, or turbulent, air on the vehicles behind, thereby allowing the vehicles to follow more closely. Front and rear wings are designed to increase downforce and create vortices, disturbing the air traveling alongside the car, which enables increased angles of attack for the rear wing. If these vortices did not exist, high rear-wing attack angles would create a significant low-pressure area under the wing, thereby increasing negative net vehicle forces and drag. While beneficial to the forward vehicle experiencing a laminar stream of air, this creates a turbulent airflow for the following vehicle. One positive performance outcome from this turbulent air flow is the “slipstream” or “draft,” where a following vehicle traveling at the same speed requires less energy to maintain its momentum. This is due to a low-pressure system behind the vehicle, which reduces the net drag forces on the following vehicle. Seems like a good thing for following vehicles, right? It is, when considering the efficiency of the battery packs used in F1 today, but this can be detrimental to downforce. For reasons previously mentioned, front and rear wings require a laminar flow of air to optimize downforce, which can be especially troublesome when braking or cornering. For example, in the 2021 design, following vehicles experience 38% less downforce when traveling within 20 meters and 46% less downforce when travel 10 meters from the forward vehicle.
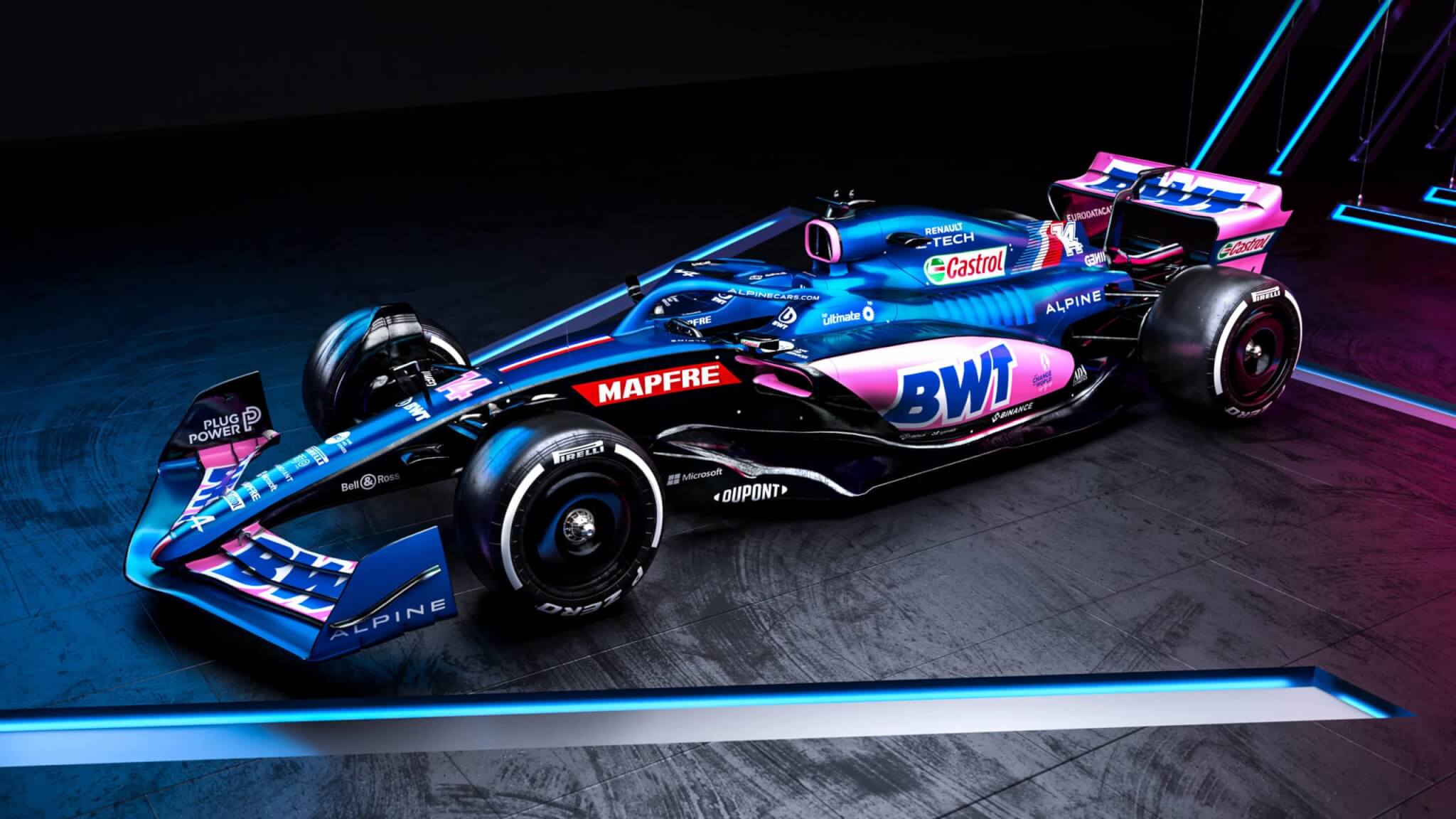
So, while the slipstream sounds great for straight-line speed and overtaking, vehicles tend to lose a large percentage of their downforce in the corners, making it difficult to overtake in those maneuvers. New aero designs will both reduce the amount of turbulent air from the forward vehicle and its effect on the follower. Significant improvements have been observed in wind tunnel and track testing that suggest only 4% downforce loss at 20 meters and 18% loss at 10 meters. This will allow vehicles to race closer together and present overtaking opportunities in multiple areas. The FiA has given the teams a considerable amount of freedom with their aero package design for the 2022 season. One example is illustrated in the vehicle’s sidepods. As preseason testing has already commenced in Barcelona, teams have been seen with different lengths, starting positions (relative to the side of the car), and opening sizes of these pods. The primary function of side pods is to funnel and guide the air alongside the car, thereby controlling the vortices created by the front wings to reduce drag. The image below (Figure 5) illustrates the pod’s opening size difference between two cars. One can also observe the difference in suspension, with one vehicle using a pull rod and the other using a push rod. Based on this image, it is reasonable to suggest that the size of the pods is designed to match the specific suspension package the team has chosen that will work with the air wakes produced by the suspension components.
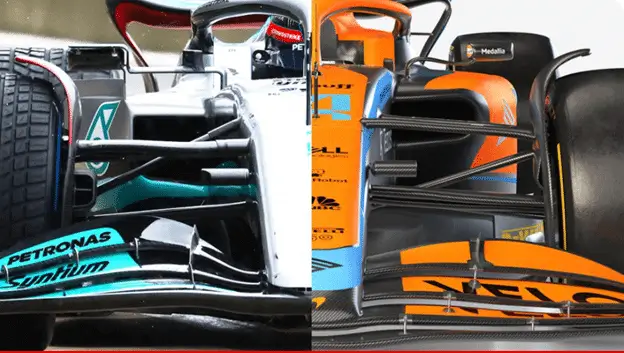
New Tires
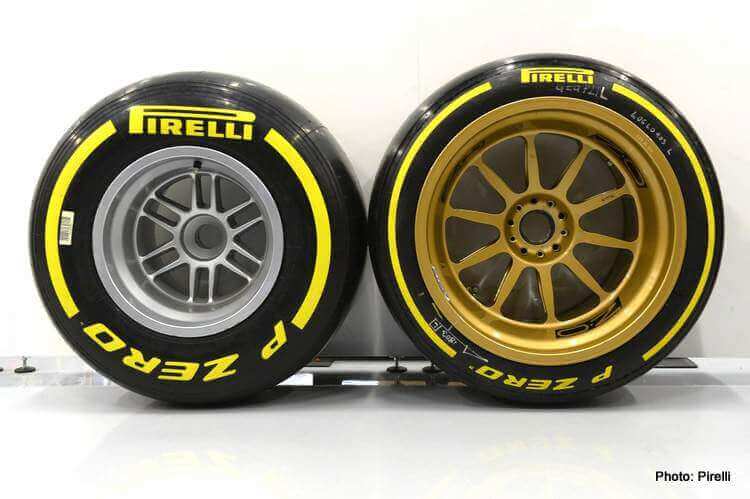
With all the discussion about the new aero package, some may be overlooking the new tire designs. Pirelli has one of its largest challenges in creating a new 18-inch diameter wheel/tire combination that exerts the same performance and durability requirements as the 13-inch tire. Increasing from a 13-inch diameter wheel, the low-profile sidewall changes the deflection characteristics in each axial plane. In other words, vertical, lateral, and longitudinal deflection and stiffness will change. The smaller volume means that less pneumatic support and more tire support is needed, which can be a challenge for durability and vehicle dynamics. Fundamentally, a stiffer sidewall will change vertical damping characteristics, lateral deflection, and relaxation lengths, all of which play critical roles in the vehicle’s response. The tire’s outer diameter will increase approximately 3 inches, increasing aerodynamic effects from the surrounding airflow. Stiffer sidewalls also yield lower shape changes, thereby changing the airflow characteristics previously seen with a larger sidewall. Additionally, engineers must solve the problem of increased rolling resistance and, with wheel/tire mass increasing, adjust their vehicle models to optimize brake balance. Overall, the new tires will offer more agility, speed, and stability to the car since the increased size and contact patch can potentially enable higher force capabilities. However, the changes to the tire’s outer profile and inner carcass present additional challenges from a thermal management perspective. The new 2022 design requires larger brakes but will also be further from the wheel due to the larger rim size, requiring engineers to factor this additional length into their thermal management strategies.
Virtual development has played a massive role in the success of the Formula One series. Technological and software advancements have made it possible to create robust tire and vehicle models in a fraction of the time that was previously needed while improving accuracy with every iteration.
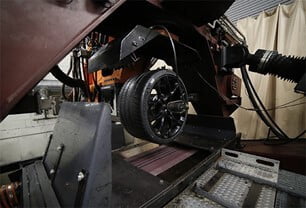
However, physical testing is required to create such models. Tire and vehicle parameterization, whether through indoor tire test labs or kinematics and compliance rigs, these tests are critical to properly characterize a system. Teams use historical data through race events, practices, and testing to apply setup configurations to the car. Since there is no historical data for the new tire designs, teams will rely on testing data from both on-track and laboratory environments. It is imperative that testing be performed at a facility containing the resources and capabilities to match the conditions seen on tracks. GCAPS has the world’s most capable flat-belt machine, offering unmatched high force, position rate, and speed capabilities. The tire’s test speed matters; do not let anyone tell you otherwise! Models created based on lower speed data require compensation in higher speed ranges, which reduces the model’s fidelity due to the increase in potential error. The GCAPS facility is manned by experienced testing staff who understand the needs of motorsports teams to improve their performance and solve critical problems. Through a multitude of testing methods, including thermal data collection and logic techniques, tire performance characterization, and drive file replays, GCAPS has designed a testing framework befitting world championship contenders.